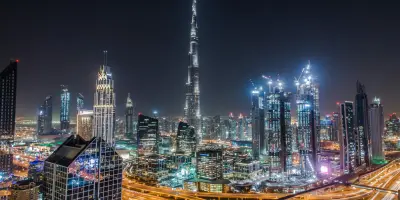
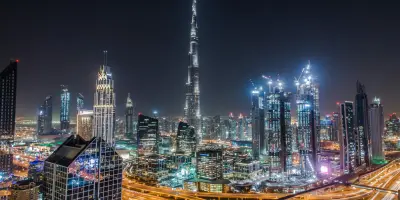

Allow access to the vendor portal for an existing record.

General Ledger, MB-310 Finance
Transfer Purchase Orders during year end process
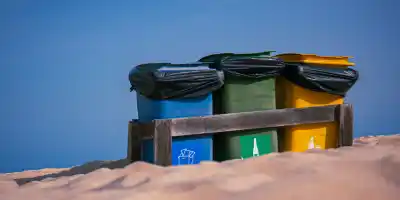
Segregation of duties

MB-300 : Foundation, User Interface Basics
Electronic Signature Dynamics 365FO
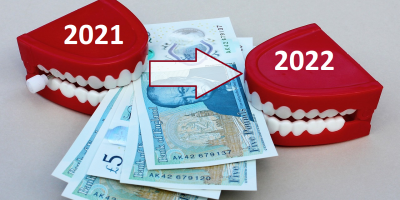
General Ledger, MB-310 Finance
Pros and Cons using year-end carry-forward budgeted POs

MB-300 : Foundation, User Interface Basics
MB-300: 1.1 Workspaces

MB-300 : Foundation, User Interface Basics
MB-300 : 1.0 Introduction
